Группа компаний «Вартон» выпускает светодиодные светильники под брендами Gauss и Varton. Их устанавливают в офисах, жилых домах, на складах и улицах — всего компания делает тысячу видов разной осветительной техники. Производство и лаборатория находятся в трёх часах езды от Москвы в городе Богородицке Тульской области. The Village съездил туда и узнал, как делают офисное светодиодное освещение.
ПРОИЗВОДСТВО
Перед зданием яркого цвета нас встречает Илья Сивцев, генеральный директор компании. В строении несколько этажей, и мы поднимаемся на самый верхний, где находятся кабинеты руководителей и шоу-рум. В нём на всех стеллажах лежат разные светильники. В целом самые распространённые лампы для освещения бывают четырёх видов: лампы накаливания, люминесцентные, галогенные лампы и светодиодные светильники. Завод «Вартон» специализируется на последних.
Сами лампочки, светодиодные модули и другие важные составляющие здесь не производят, а закупают их в Китае, Корее, Финляндии и Австрии. «Чем дальше ты уходишь внутрь, тем ты более медленный и неэффективный», — поясняет Илья. Все эти предприятия собирают лампочку из нескольких элементов: базы (пластиковая деталь, внутри которой — алюминий), цоколя и светодиодного модуля и, наконец, драйвера, который отвечает за свечение. Сверху на эту конструкцию одевается рассеивающий элемент (чаще всего из пластика). Поэтому здесь делают корпуса для ламп, рассеиватели, собирают всё вместе и отгружают поставщикам. Ещё здесь есть лаборатория, на которой тестируются разные лампы и светильники.
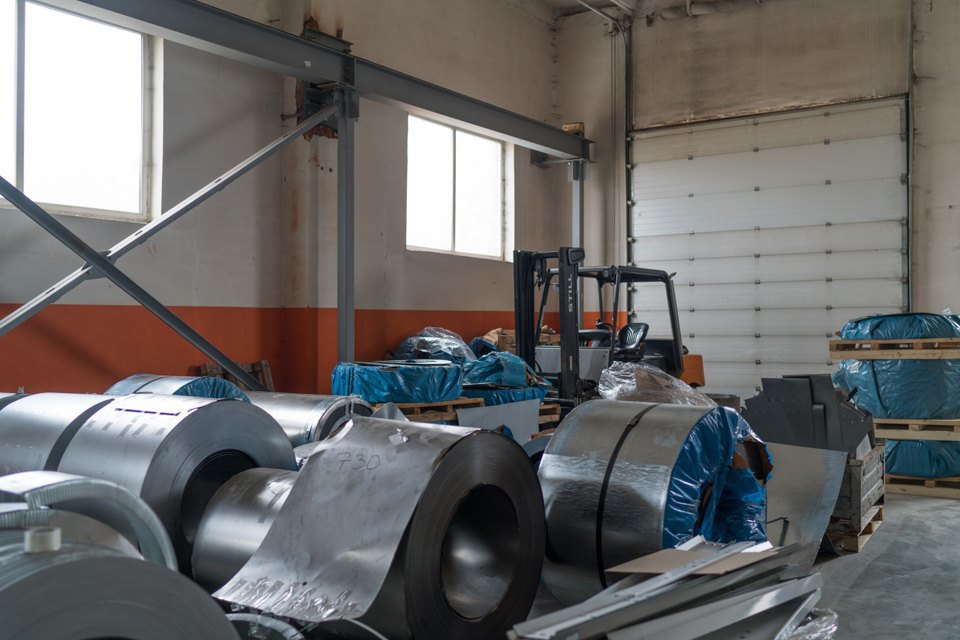
ПРОИЗВОДСТВО КОРПУСОВ
Весь процесс начинается с производства металлических корпусов для светильников. Металл поступает в огромных рулонах, самый тяжёлый из которых может весить 4,5 тонны. Затем такую катушку поднимают на кран-балке и переносят на размотчик. Главная его цель — медленно разматывать полотно металла и подавать его на автоматическую линию, первая операция которой — правка. С помощью аппарата, который напоминает устройство для отжима белья на старых стиральных машинах, листы металла делают абсолютно ровными, плюс установка ориентирует поток, чтобы он правильно вошёл на следующую станцию.
А дальше в металле автоматически вырубаются все нужные отверстия автоматическим штампом. После этого гильотина резко, с шумом отрезает кусок рулона нужной длины, и он едет на станцию гибки, где машина загибает длинные бортики будущего корпуса, складывает их как конверт. Робот берёт эту конструкцию и переворачивает, чтобы уже другая машина загнула торцы корпуса: это называется «станция подгиба язычков». Линия завершается клинчингом — так называется метод крепления металла с металлом без сварки и лишних заклёпок и болтов. Получается такой зацеп, который сам себя держит. Так, каждые 17,3 cекунды каждый конвейер готовит новое изделие, сотрудник его забирает и складывает в высокие стопки, как в игре «Дженга».
Всё оборудование — в сенсорах: если готовый корпус не убрать с линии, то машина остановится и будет ждать до тех пор, пока изделие с него не снимут. Так делают массовые партии на двух линиях.
С эксклюзивными и пробными экземплярами приходится повозиться подольше: хоть процессы всё те же самые, но оборудование уже другое. «Аккуратно, он может ударить», — предостерегает нас Илья. Мы отходим на пару шагов от аппарата: платформа постоянно движется и может быстро разогнаться, поэтому на полу есть разметка, за которую заходить запрещено. На этой автоматической машине — координатно-пробивном прессе — в листах металла делают отверстия, а после несут на листогиб, который всё делает сам — сгибает, переворачивает, — стоит лишь выбрать нужную программу. Среди процессов есть и те, что нужно делать вручную; такая линия нужна заводу для эксклюзивных небольших серий.
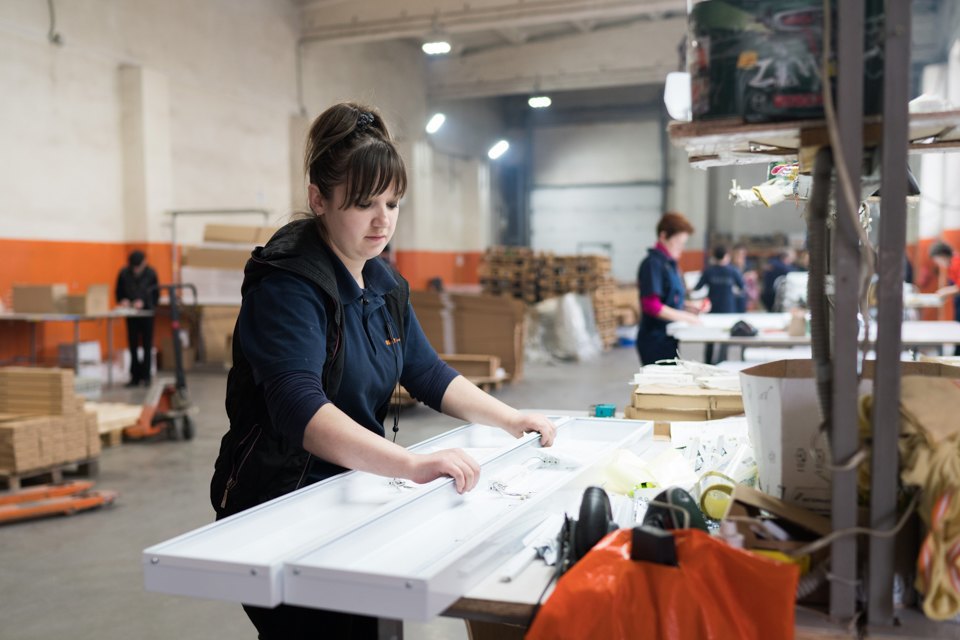
ПОКРАСКА
Готовые корпуса будущих светильников красят на оборудовании, похожем на карусель: на проволоку подвешивают корпуса на крючках, и они медленно едут от одной станции к другой. Начинается всё с мытья: специальный душ с химическим раствором удаляет масло с металла, затем корпуса попадают в сушилку, где при температуре 280 градусов вода с поверхности улетучивается. Остыв, они попадают в камеру порошковой покраски: там стоят автоматические пистолеты, которые перемещаются сверху вниз и покрывают корпус ровным слоем краски. Правда, в углы такая краска не попадает, поэтому в камере ещё работает сотрудник в специальном костюме и прокрашивает то, до чего не удалось дотянуться автоматическим пистолетам. Краска тяжёлая, и она будто сама прилипает к поверхности; если же этого не случилось, то напор воздуха внизу камеры всасывает её через отверстия в полу и снова подаёт на покраску. Затем краску нужно «запечь», поэтому детали отправляются в печь полимеризации. Размер камеры таков, что весь путь изделия от начала до конца занимает около 20 минут. Всё, корпус готов, теперь его можно снимать с крючка и отдавать на сборку.
СБОРКА
Илья Сивцев рассказывает, что сборкой занимаются две бригады, в одной из которых преобладают мужчины, в другой — женщины. Первые берут на себя тяжёлую работу, предпочтительно в малых эксклюзивных сериях, а женщины, по его словам, хорошо справляются с поточной работой — там, где нужна скорость и чёткость. Суть одна и та же: в покрашенный корпус вставляют модули, драйвера, подключают драйвера к клеммной колодке, через которую попадает ток. В основном всё собирается вручную, иногда используется шуруповёрт.
Но от креплений вроде болтов и шурупов в компании стараются отказываться в пользу снэплоков: так детали можно цеплять к нему прямо на корпус. Во время сборки на каждом столе попеременно загораются светильники — сотрудницы проверяют работоспособность каждого изделия. Всё это делается вручную, потому что в ассортименте завода больше тысячи позиций, а автоматизировать такое количество изделий сложно. У сотрудников есть свои нормативы по сборке: например, дневной стандарт для одного сборщика — это 363 изделия. В целом завод стремится к тому, чтобы каждые восемь секунд выдавать готовое изделие.
Те модели, что собирают в смену, зависят от заказа: во время нашего посещения собирали медицинские (они герметичны), аварийные (продолжают работать ещё три часа после того, как отключили электричество) и поточные (для пополнения склада). На каждом светильнике должен быть рассеиватель, которых на заводе выпускают пять видов — например, «призма», «опал», «колотый лёд». Рассеиватели сборка не надевает на светильник, а только упаковывает, так как заказчик выбирает ту модель, которая ему нужна. Рассеиватели поступают на завод в виде крупных листов поликарбоната, которые нарезают на пласты нужного размера.
Некоторые корпуса светильников делают пластиковыми — такие модели обходятся дешевле, поэтому модель можно наверняка увидеть чуть ли не в каждом подъезде. Их производят в цехе, где стоят термопластавтоматы. Происходит это так: сверху в машину засыпают пластик в гранулах, который позже автомат плавит. Все детали рождаются в пресс-форме, состоящей из двух частей, и когда они смыкаются, подаётся горячая пластиковая масса при температуре 300 градусов. Форма открывается, а робот достаёт получившееся изделие наружу — всё это занимает 98 секунд. Потом рассеиватели сотрудник вручную разъединяет и чуть подравнивает место разлома.
На этом же заводе производят уличное освещение. «В разработке они сложнее, но производство их простое», — рассказывает Илья. Светильники готовят из огромных алюминиевых балок, длина которых может достигать шести метров. На специальном оборудовании балку под высокой температурой прогоняют через пресс, внутри которого есть форма — фильера, отвечающая за направление среза. Затем сотрудники в ней делают отверстия и режут на куски нужного размера с помощью циркулярного ножа.
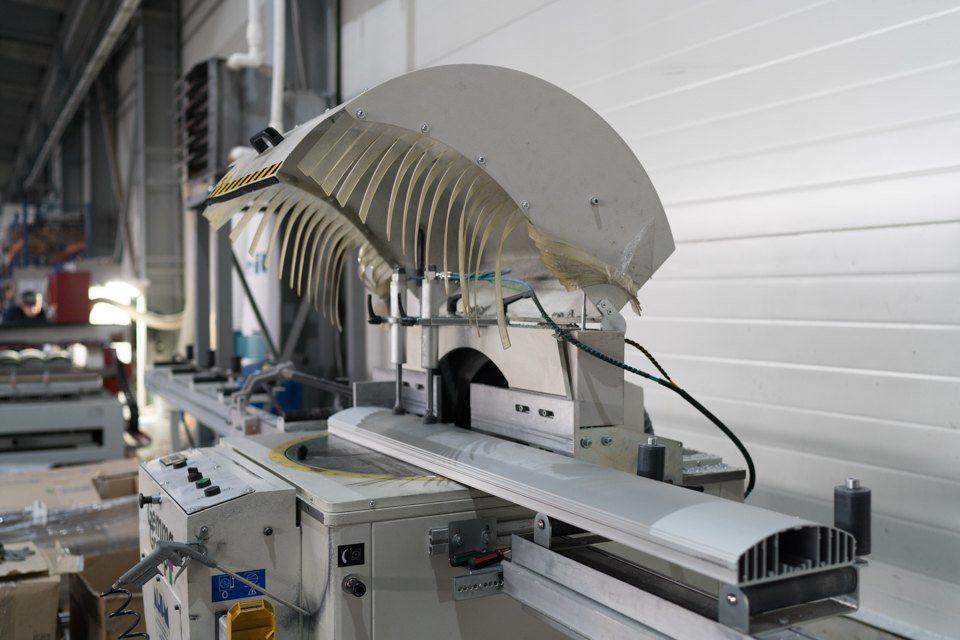
СКЛАД И ЛАБОРАТОРИЯ
Часть готовой продукции попадает на склад размером 3 500 квадратных метров. Всего на складе около 2 тысяч палето-мест. Рядом со складом находится лаборатория завода, где сотрудники проверяют продукцию на прочность и исследуют лампочки, которые закупают у поставщиков.
Первое, что бросается в глаза, когда заходишь в лабораторию, — огромный шар с открытыми створками. Это фотометрический шар, в котором производятся все измерения и проверяются технические характеристики светового прибора. В основном здесь тестируют лампочки: их вкручивают в центр, закрывают и считывают все нужные показатели.
Дальше у стены установлены стеллажи с включёнными лампами — это деградационные стенды. Свет от них такой яркий, что кажется, будто находишься в фотостудии на съёмке. Оказывается, все эти лампочки светят круглосуточно — так сотрудники лаборатории проверяют, насколько долго будет работать лампа и как эти показатели отличаются от заявленных. Плюс на протяжении всего срока службы работники снимают показания с каждой лампы, отмечая, как они меняются с течением времени. Если сотрудники увидели, что через тысячу часов лампа села, то это знак, что нужно проверить всю партию ещё раз.
На этом испытания светильников не заканчиваются. Следующая машина позволяет проверить лампочку на пылезащищённость, её задача — посыпать объект пылью (эту роль играет тальк). Дальше идут климатические камеры, в которых можно установить разные температуры — как самые высокие, так и низкие — и посмотреть, как при них будет вести себя лампочка.
Площадка одного из тестов похожа на бассейн: и стены, и пол вымощены плиткой. Здесь проверяют, насколько светильник устойчив к воде. Один из тестов выглядит так: светильник закрепляют на специальной платформе, которая вращается, а в это время на неё из крана, похожего на пожарный, бьёт сильный поток воды (степень напора можно менять).
Но самое интересное в лаборатории — это отдельная комната, где стоит прибор, помогающий измерить кривую света (то, как будет светить лампа) и другие светотехнические параметры. Помещение большое (18 метров в длину и 6 в высоту), полностью чёрное: и стены, обитые бархатистым материалом, и потолок, и даже батареи здесь чёрные. На входе в комнату установлен столб с несколькими зеркалами и балкой, которая вращается, а наверху установлен прибор с тремя детекторами — один отвечает за цвет, и два — за свет. Испытания проходят в два этапа: в центре устанавливается светильник на специальной раме, и когда начинается тест, то рама эта вращается, штанга с детекторами вращается вокруг светильника и в разных плоскостях измеряет его.
Сейчас завод производит около 1,5 миллиона светильников в год, продавая их заказчикам из России, стран СНГ и некоторых европейских стран. Есть клиенты и из Африки — например, Нигерии и Египта.
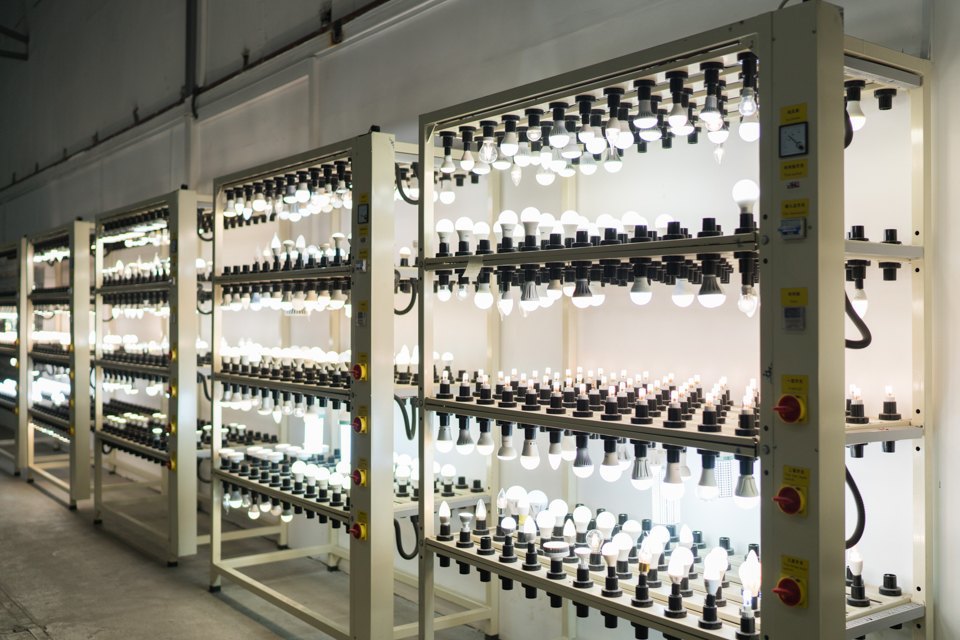
Комментарии 0